Plastics Industry
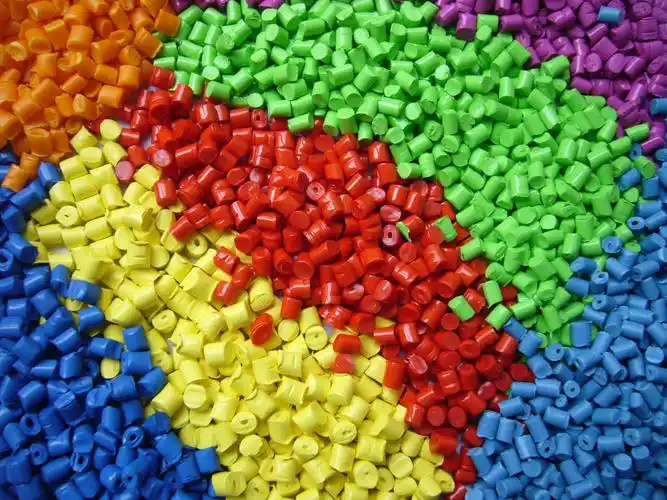
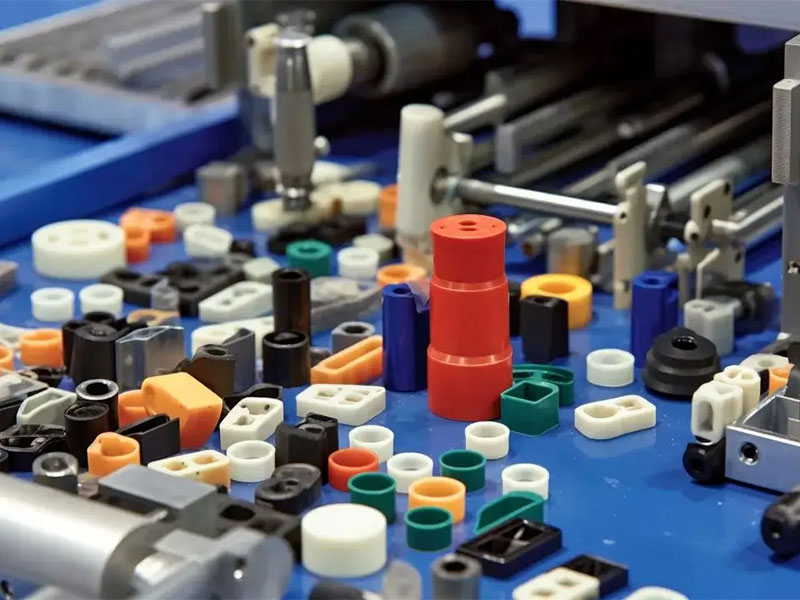
Humidity/Process Requirements
Target Humidity Range: 35~50% RH
Challenges
Humidity control is crucial in the plastics industry, as excess or fluctuating moisture levels can lead to defects in production and compromised product quality:
Material Degradation: Plastic resins are hygroscopic and absorb moisture, which can cause hydrolysis during processing, leading to weakened mechanical properties.
Defects in Molding: Excess humidity creates bubbles, voids, or warping in molded plastic products, resulting in higher rejection rates.
Corrosion of Equipment: Moisture can corrode injection molding machines, extrusion equipment, and other machinery, increasing maintenance costs.
Static Electricity: Low humidity environments may cause static buildup, affecting precision in production processes.
Solutions
Rotary dehumidifiers offer precise humidity control to address these challenges effectively:
1. Moisture Removal from Raw Materials:
Maintains optimal low-humidity levels, preventing moisture absorption in plastic resins and ensuring consistent product quality.
2. Prevention of Defects:
Ensures uniform drying and molding conditions, reducing defects like warping, bubbles, or cracks in finished products.
3. Corrosion Protection:
Protects machinery and equipment from moisture-related corrosion, extending operational life and reducing downtime.
4. Enhanced Production Efficiency:
Stable humidity control improves the flow and processing of plastic materials, ensuring smooth operations and reduced waste.
5. Static Control:
Maintains the right balance of humidity to prevent static buildup, improving precision in automated processes.
Rotary dehumidifiers are indispensable in the plastics industry, ensuring superior product quality, reduced defects, and efficient production processes.