Rubber Industry
Used in the storage and processing of rubber to prevent rubber from aging and deformation.
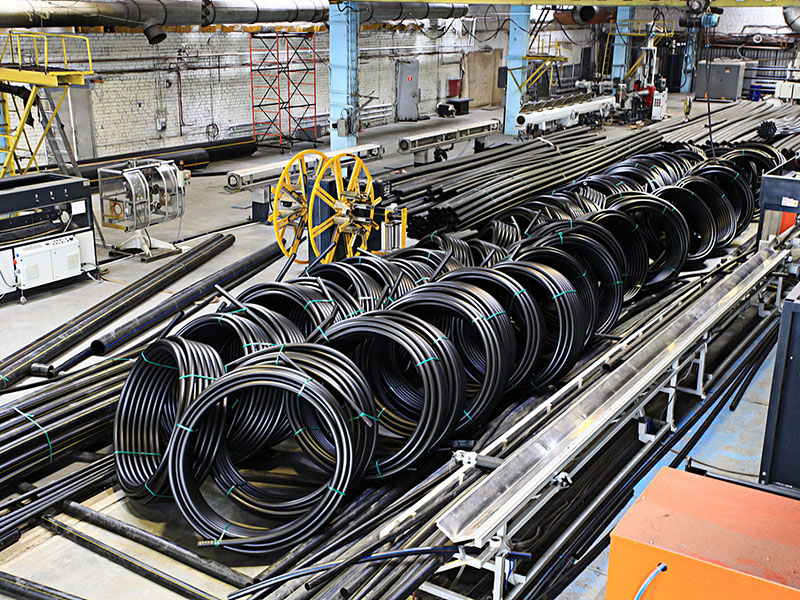
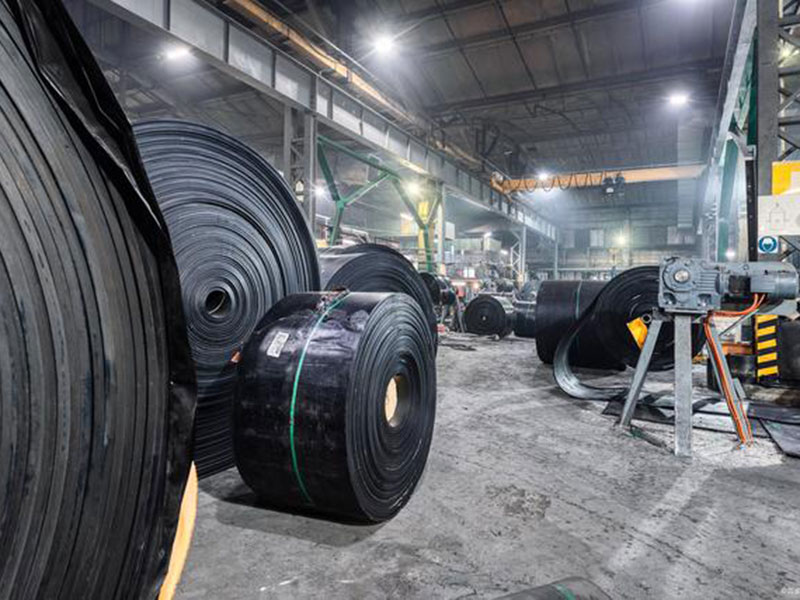
Humidity/Process Requirements
Target Humidity Range: 40~60% RH
Challenges
Humidity control is vital in the rubber industry to ensure product quality, efficient processing, and the durability of both raw materials and finished goods:
Material Degradation: Excessive moisture can cause rubber compounds to absorb water, leading to reduced elasticity and performance.
Defects During Curing: High humidity disrupts the curing process, resulting in uneven hardness, shrinkage, and surface imperfections in finished rubber products.
Corrosion of Machinery: Humid conditions accelerate corrosion of molding machines, extruders, and other processing equipment, increasing maintenance costs.
Mold and Mildew Growth: Raw rubber stored in high-humidity environments is prone to microbial growth, which can degrade materials.
Solutions
Rotary dehumidifiers provide precise humidity control to address these challenges effectively:
1. Improved Material Quality:
Maintains low-humidity levels to prevent water absorption in rubber compounds, preserving elasticity and performance.
2. Defect-Free Curing:
Ensures consistent curing conditions, reducing shrinkage, bubbles, and other defects in finished products.
3. Machinery Protection:
Reduces moisture-related corrosion in machinery, extending equipment lifespan and minimizing downtime.
4. Preservation of Raw Materials:
Controls storage conditions to prevent mold and mildew growth, ensuring the quality of raw rubber materials.
5. Enhanced Production Efficiency:
Stable humidity control ensures smooth processing and reduces waste caused by defective products.
Rotary dehumidifiers are a critical solution for maintaining product quality, operational efficiency, and material longevity in the rubber industry.