Ship Painting Industry
In the secondary rust removal operations in the shipbuilding and ship repair industries, rotary dehumidifiers are indispensable air treatment equipment.
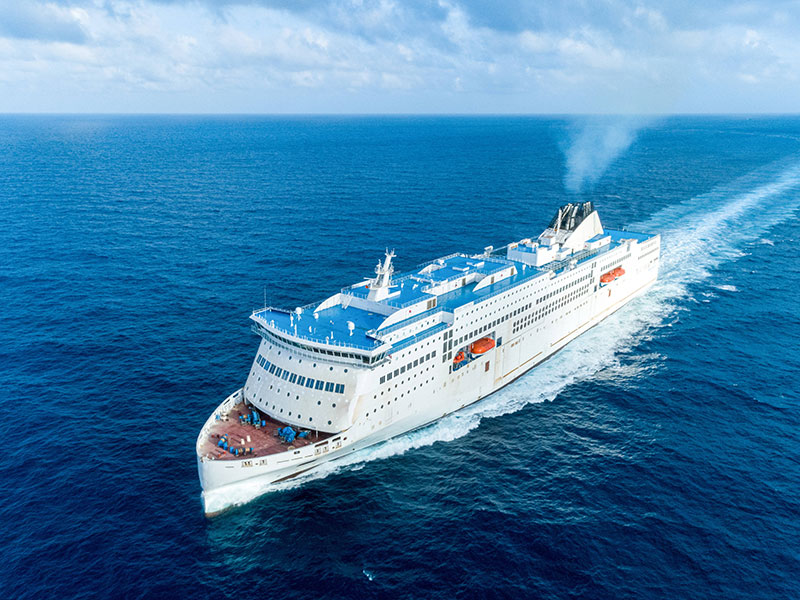
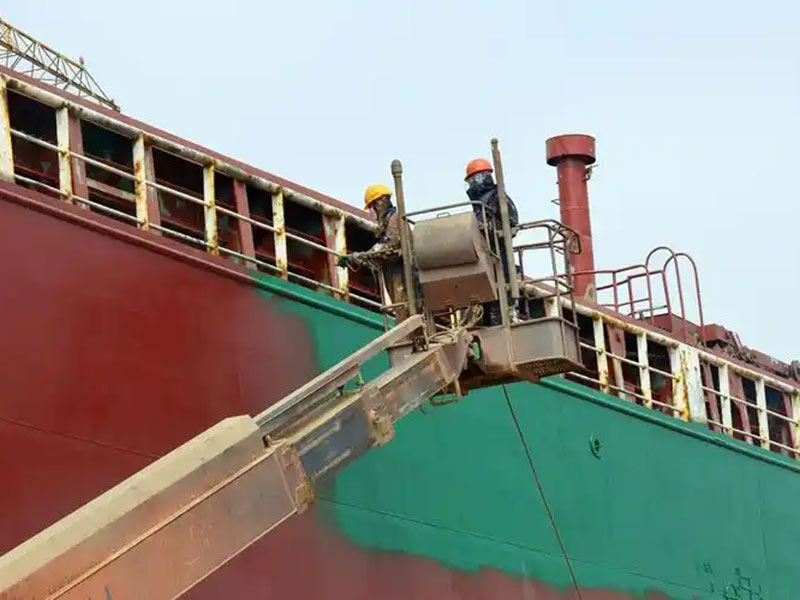
Humidity/Process Requirements
Target Humidity Range: 40~60% RH
Challenges
Humidity control is essential in the ship painting industry to ensure smooth application, durability, and quality of protective coatings. Improper humidity levels can lead to several issues:
Condensation on Surfaces: High humidity causes condensation on ship surfaces, preventing proper adhesion of paint and coatings.
Coating Defects: Excess moisture leads to blistering, peeling, and cracking of coatings, reducing the lifespan of protective layers.
Corrosion: High humidity accelerates corrosion on metal surfaces, undermining the integrity of uncoated or inadequately coated areas.
Drying Delays: Improper humidity levels slow down paint drying, leading to production delays and increased costs.
Solutions
Rotary dehumidifiers provide effective solutions for maintaining optimal environmental conditions in ship painting processes:
1. Condensation Prevention:
Keeps surfaces dry by maintaining stable humidity levels, ensuring proper paint adhesion.
2. Improved Coating Quality:
Controls moisture to prevent blistering, peeling, and cracking, resulting in durable and long-lasting coatings.
3. Corrosion Protection:
Ensures low-humidity conditions to prevent rust formation on exposed metal surfaces before and after painting.
4. Faster Drying Times:
Speeds up drying and curing processes by maintaining optimal humidity, reducing production delays.
5. Energy-Efficient Operation:
Rotary dehumidifiers consume less energy while delivering precise control, lowering operational costs.
Rotary dehumidifiers are a vital tool in the ship painting industry, ensuring high-quality finishes, preventing corrosion, and improving overall efficiency.